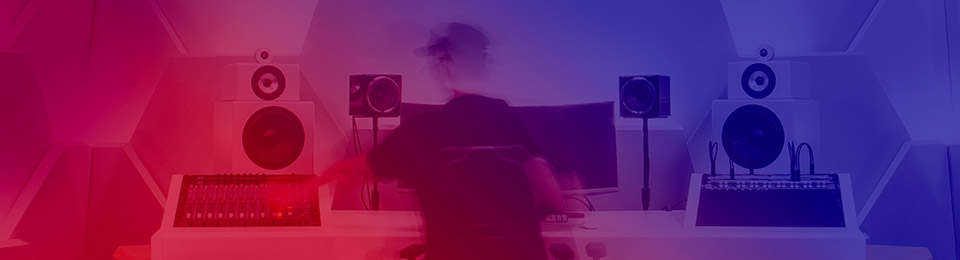
Blog
True love for great sound unites us.
Blog
True love for great sound unites us.
What does it take to design the ultimate live microphone? Lots of live experience, embodied by our product manager Roman Jagl.
We sat with Roman to discuss the MTP W950 from idea to execution. Read on to learn more about how we brought studio sound to the stage.
This recorded interview has been edited for length and clarity.
I'm a product manager and joined the company three years ago. Before that, I was already in touch with the company as a beta tester, and I have happily used many LEWITT models for countless tours.
I'm still working as a self-employed audio engineer, but before that, I was a full-time engineer. Now as a product manager, I consider which product features are valuable to the end user to create a fantastic user experience.
My focus is on live sound. I started with SAE (School of Audio Engineering) and finished my audio engineering degree there. When I was in school, I was already very oriented toward music. But although I always liked playing music, I wanted to make recordings happen in the studio. Somehow, things worked out differently than planned, and I stumbled into the live scene, and I was lucky that my first gig was the Deep Purple European tour. Not bad!
In the beginning, we thought we could just take an existing handheld mic, cut off the handle, put the PCB in, and make it wireless compatible, and that's it.
The core team of the development in the first phase was small. It consisted of Devid (acoustic engineer), Alessandro (mechanical engineer), Arnaud (electronic engineer), and me, managing the project.
Later the full team grew to 18 members.
With MTP W950, we wanted to create a microphone that solved common issues and was easier for vocalists to use, and as some of us have a lot of experience as live engineers, we are in a good position to see those issues firsthand. Early on, we decided on four major areas to focus on:
Consistent sound wherever you perform
If you go to a rehearsal room, you don’t have much space for setting up a wireless system. So you prepare your show with a different microphone, and maybe you get used to that sound. But ultimately, you end up using a different microphone you're not familiar with just to be able to go wireless.
It makes most sense, if you do your rehearsals and gigs with the same microphone. Wired or wireless.
The goal was to offer excellent sound quality in the studio or the rehearsal room and have it fully transferable to the stage without compromises.
Deal with bleed
Artists move around onstage and might get close to the drum kit as they perform and then you suddenly have a lot more drums in your mix. Bleed from other sources is one of the main issues you must deal with as a live engineer, especially on big stages
With MTP 950, we wanted to reduce bleed to an absolute minimum. It's better for the live sound engineer, better for the performer, and most importantly better for the audience.
The lead local has to be upfront, and for modern-sounding, denser mixes, you are compressing the vocals very hard. You must push it to cut through the mix as you are going very loud. The more you compress it, the louder everything else gets that you don't want to have in your mix. It gets even worse if you're adding reverb or delay on top of the vocals. Things get difficult quickly. That's why I wanted this microphone to be as immune to bleed as possible.
Make it cupping-safe
Another problem we address with the MTP W950 is cupping. Cupping drastically changes the sound, and not in a good way because you lose directivity. The more you cup the mic, the more a cardioid pattern becomes an omni. You will run into feedback problems, and again you will pick up other sound sources on stage.
LEWITT uses a cupping-safe design so you can hold the microphone very high on the basket before it changes tone. Additionally, there’s a natural barrier on the head basket to resist the tendency to grip further up, which is a thing rappers do often.
Make it weatherproof
Many vocalists perform outdoors, even in the wind or the rain. Moisture buildup in the capsule can cause high frequency loss, and sudden wind gusts cause momentary bass buildup that can overload a sound system. So we needed to make a microphone suitable for use in all these conditions.
We added a second capsule layer with a dome shape with no flat surface for the water to stick on. This also results in very good wind performance and incidentally minimizes "structure-born" noise, which is the sound of the internal components.
Challenges
It was an easy idea at the beginning. Just take an existing model, the MTP 940 CM, and optimize the polar pattern performance. In the end, it was a very tricky task to do. We had to completely change the capsule's design and reduce the amount of material to an absolute minimum.
Finding the right materials was also a challenge. Coming from this 3D printed prototype of the idea, finding the perfect produce materials (the right rubber, etc) was challenging.
Solutions
With the help of 3D printing, it was quite easy to understand how to solve the problems. Our first prototype was a 3D print, but you could use it, and we could mount it on a wireless transmitter. And it even had a working screw mount, which was impressive from a 3D print.
And I think at that point I realized, okay, this is turning out to be something outstanding.
In the end, we made one of the most durable live microphones ever.
Drop tests
We put quite a lot of hard work into drop testing because the last thing that you want in a live situation is for your microphone to be destroyed by it slipping out of the hand.
So we started with the two-meter-high drop test to see where the weak points were, and then changed the parts that weren't passing the test. We also would redesign the microphone mechanically so that it can take more stress.
Now, this mic is designed to withstand at least six falls from a 2-meter height on each side, rotated 45 degrees each time, and then two more falls against the front and back.
Pressure tests
We tested the MTP W950 with the loudest sources we could find.
We had to ensure the microphone could hold extremely high sound pressure levels. Part of this involved getting loud vocalists, so we invited screamers from metal bands to use it onstage. We had some of the loudest screamers in the world come and put it through its paces.
We also invited a trumpet and trombone player to perform. In the end, the trombone won by far at around 150dBSPL. With the attenuation activated, the MTP W950 can handle sound pressure levels up to 152 dBSPL.
Environmental tests
We used a “spitting robot” that constantly sprays the mic for two hours. This is in addition to our standard climate chamber test that it had to pass. We also would submerge the capsule in water to see if it's still working.
One funny story, was last winter, when I brought the cold microphone from the car on the stage, the condensation changed the sound, and then it needed some time to recover so that the water evaporated and the sound returned to where it should be. This helped us make even more adjustments to make it weather resistant.
Last year, we put the MTP W950 in the hands of vocalists all over the world.
Why run a beta?
With the prototypes, we tried to put the MTP W950 into real-life situations as best we could. We have a great studio in our office, but we do not always have access to a stage or a live audience, let alone a whole concert venue where the microphone was meant to be used the most.
We got the contacts of live sound engineers that were interested and they used the MTP W950 for their tours before its release, including Kehlani, T-Pain, and The Rolling Stones.
What we learned from the beta
The response from the beta was very positive, praising how easy it was to create great mixes and, of course, the wireless-compatible capsule.
The microphone performed exceptionally, with the only issue being some paint chipping on the pre-production models. This was due to the plating material we used to reduce electrostatic noise interference. It was a simple matter of adjusting our manufacturing process to make the paint stick better to the plating.
But overall, everyone who used the microphone was super excited, confirming our approach.
What excites me the most about the MTP W950 is that it solves so many problems I've had to deal with for over 20 years as a live engineer.
This microphone made my life a lot easier. And I hope that everybody who's using the microphone sees it the same way.
As a live sound engineer, I have to say; it was never that easy to get vocals in front of a mix. Have fun with the product. I am sure you'll like it as much as I do.